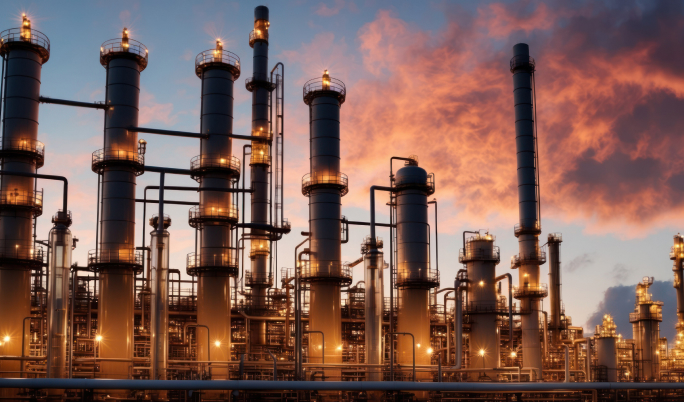
Saturday, August 31, 2019
H2S Mitigation Technologies for Gas
Managing H2S is a challenge at every stage of gas operations. H2S mitigation techniques are implemented in order to preserve…
Q2 Technologies Team
Experts in H2S Scavenging Solutions
With decades of combined experience, the Q2 Technologies team specializes in innovative hydrogen sulfide (H2S) scavenging solutions for the oil and gas, wastewater treatment, and industrial sectors.
3 Questions about H2S: Why, When and Where
Approximately 90 percent of the sources that emit hydrogen sulfide into the air are natural such as the decomposition of dead plant and animal material. Hot springs and volcanos also emit H2S.
Sources of H2S in Natural Gas
Hydrogen sulfide is a naturally occurring component of natural gas since it is a product of thermal conversion of decayed organic matter. Natural gas is about 70 to 90 percent methane and up to 20 percent of other hydrocarbons like butane, propane and ethane. There are contaminants naturally present in natural gas too such as water vapor, sand, oxygen, carbon dioxide, nitrogen, helium, neon and hydrogen sulfide. In fact, hydrogen sulfide is the predominant impurity in natural gas. Natural gas is classified as sour when H2S is present in amounts greater than 4 ppm.
Figure 1.- H2S and Treatment Spots along Gas Processing Line
Anthropogenic Releases of H2S in Gas Operations
Anthropogenic releases of H2S into the air result from industrial processes such as in natural gas operations including its extraction, transportation, storing and processing. Figure 1 shows the stages of gas production where H2S might be released and/or treated. Hydrogen sulfide may be released into the atmosphere at wellheads, pumps, piping, separation devices, oil storage tanks, water storage vessels, and during flaring operations. Flares burn gases that are not to be sold as shown on Figure 2, or where operating problems may occur. Sulfur dioxide (SO2) is the product of combusting hydrogen sulfide, but in the event of incomplete combustion, H2S may also be emitted into the atmosphere.
Figure 2.- Typical Flaring of Gas in the Field
H2S Concentration and Prone Regions
Between 15 to 25 percent of natural gas in the US may contain hydrogen sulfide, while worldwide, the figure could be as high as 30 percent. Figure 3 shows the major H2S prone regions within the continental US. The regions with the largest percentage of proven reserves with at least 4ppm hydrogen sulfide are Eastern Gulf of Mexico (89 percent), Overthrust (77 percent), and the Permian Basin (46 percent).
Common H2S Mitigation Techniques
Sour gas is routinely ‘sweetened’ through different H2S mitigation techniques. Ninety five percent of the gas sweetening process involves removing the H2S by absorption in an amine solution, while other methods include carbonate processes, solid bed absorbents, and physical absorption.
Figure 3.- H2S Prone Regions within Continental US
There are some environmental regulations for controlling emissions from major sources of H2S and it is also regulated as an occupational hazard. Additionally, H2S is corrosive and it needs to be removed. Gas is routinely tested to determine H2S concentration. Once H2S testing has been performed, it is necessary to mitigate its impacts and bring the gas to the desired specifications. There are mechanical/operational (physical), biological and chemical mitigation techniques from which engineers choose according to gas characteristics, H2S concentration, economic considerations, and other variables. Hydrogen sulfide is not found in isolation but together with methane, hydrogen and higher hydrocarbons, and traces of nitrogen-, oxygen- and metal- containing species which complicate the selection of the most suitable H2S mitigation technique.
Managing H2S is a challenge at every stage of gas operations. H2S mitigation techniques are implemented in order to preserve the environment, take care of workers, avoid corrosion and bad smells, and protect the value of products. In selecting a gas sweetening process, responsible engineers need to consider many variables such as gas stream pressure, impurities present in the feed gas, composition of the acid gas and quantity of sulphur to be removed.
Mechanical/operational H2S mitigation techniques
When natural gas is produced as a byproduct of oil extraction, operators will often vent or flare the gas. Flaring is the practice of burning gas that is deemed uneconomical to collect. Flaring is also used to burn gases that would otherwise present a safety problem. It is common to flare natural gas that contains hydrogen sulfide, in order to convert the highly toxic hydrogen sulfide gas into less toxic compounds. Venting is the direct release of methane gas to the atmosphere. During oil development, gas may vent to the atmosphere. The solids and fluids from the well go to the pits, while the gases are allowed to escape to the atmosphere, or they are flared.
Physically, stripping is a very common alternative to remove H2S. The oil industry often uses a nitrogen stripping system to remove the H2S. Nitrogen is an inert gas that prevents the flammable gases from igniting and thus eliminates the risk of explosion. Once the H2S has been separated from the gas, it can be converted to a waste product that can safely be disposed of or it can be used in the manufacturing of sulphur. However, it is difficult and costly to transport the liquid nitrogen that stripping systems need.
Membrane technology could offer a solution for the nitrogen transportation hassle that some sour crude treatment facilities require. In this case, compressed air is pushed through a set of polymer fibers or the membrane. As the compressed air moves through the membrane, the nitrogen molecules are separated from the other molecules.
Biological H2S mitigation techniques
These are used to remove H2S from water in wastewater treatment plants but not for gas at the moment.
Chemical H2S mitigation techniques
Additives to treat H2S in gas are very diverse and work in different forms. The caustic soda wash is one of the oldest chemical absorption processes for removing small quantities of CO2 and H2S from natural gas and refinery gases. The Iron Sponge process is another old scavenger used to remove H2S and mercaptans from natural gas though it is difficult to dispose of spent Iron Sponge. SulfaTreat is a dry, free-flowing iron oxide based media that selectively removes H2S and some light mercaptans from vapor and liquid streams but is limited to wet gas streams. The reduction in concentration of hydrogen sulfide might follow the absorption route, such as alkanolamine, ammonia solution and alkaline salt solutions; and oxidation of H2S using iron oxide, activated carbon or a Claus process.
H2S mitigation technologies are not mutually exclusive and a combination of techniques might be used.
On Table 1, we show the different chemical additives that are commonly used for H2S removal from gas including our dry media Pro3® Nano and our custom formulated MEA triazines.
Table 1.- Chemical H2S Scavengers for Gas
Q2 Technologies’ Solutions for H2S Mitigation
Whether you need to mitigate H2S at the wellhead, during storage, transportation, or processing, we at Q2 Technologies can help you treat your gas and get more bang for your money. We offer our Pro3® Nano and are reliable manufacturers of triazine-based scavengers, which will bring your gas to specs and are custom formulated according to your needs. For more details on H2S removal technologies, check out our H2S removal solutions for crude oil. Contact us today to discuss how we can serve you.
FAQs
Hydrogen sulfide (H2S) is highly toxic and corrosive. It poses serious health risks to workers, can cause equipment damage, and leads to environmental hazards if not properly managed.
Flaring burns off H2S and other harmful gases, reducing their release into the atmosphere. It is a critical safety measure during emergencies or when processing equipment is offline.
Decisions depend on factors like H2S concentration levels, operational conditions, regulatory requirements, and cost considerations. The right technology balances effective removal with safety and economic efficiency.
Related Articles
HOW CAN WE HELP?
Have a question? Need a quote? Our technical staff is here to help you identify the right solution for your project requirements.