Q2 Technologies has brought to market Pro3® Nano, a proven non-triazine solid catalyst and engineered reactor system, designed to treat for Hydrogen Sulfide (H2S) in Natural Gas. When loaded into specially designed reactor vessels or retrofitted contact towers, the Pro3® Nano product can offer lower operating costs as compared to triazine scavengers or other solid bed media. With longer cycle times, allowing for fewer cleanouts, and less field personnel on hand to monitor on a daily basis, operations utilizing Pro3® Nano add value to reserves by increasing production of previously curtailed sour wells.
CHALLENGES
- Q2 Technologies was approached by a midstream customer who was gathering and proccesing sour gas and it needed to meet pipeline specifications for H2S.
- 1.2 MMscf/d at 4000 ppm, commercially seeking 4 ppm, which is pipeline quality.
- Customer requested a non-liquid alternative to get away from the commodity-based triazine citing seasonal economic swings and the operational challenges that often plague gas streams when treating with triazine such as fouling and scaling.
SOLUTION
- We identified Pro3® Nano because the solid media competitor base was simply not achieving pipeline quality specifications.
- Pro3® Nano reactions were immediate and maintained 0 ppm for an extended period of time. When breakover did occur with Pro3® Nano, the process was gradual as compared to the others.
BREAKOVER H2S IN STRESS COMPARISON STUDY
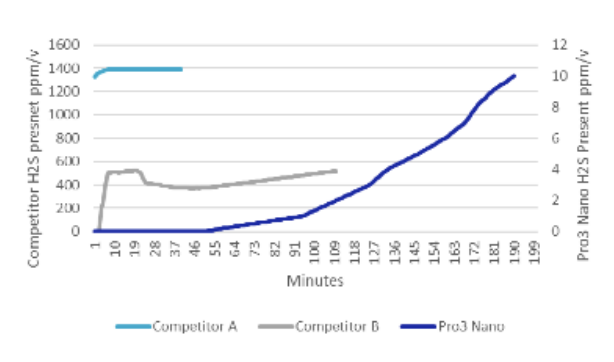
Pro3® Nano outperforms competitors significantly, as shown in this example lab trial. Samples were dosed at extremely high levels of H2S and Pro3® Nano maintained 0 ppm for a period of time and when breakover occured, it was gradual.
For the 1.2 MMscf/d example, we utilized a lead/lag configuration in our design. This setup included a coalescer upstream of the reactors which provided additional filtration. The lead/lag concept allows for continuous operations based on Q2 Technologies’ extensive field development program. Accounting for the expected breakover, the robust design of the lead/lag unit can be switched out so the lag reactor becomes the new lead reactor. The ability to swap reactors increases the bed life of the overall catalyst system.
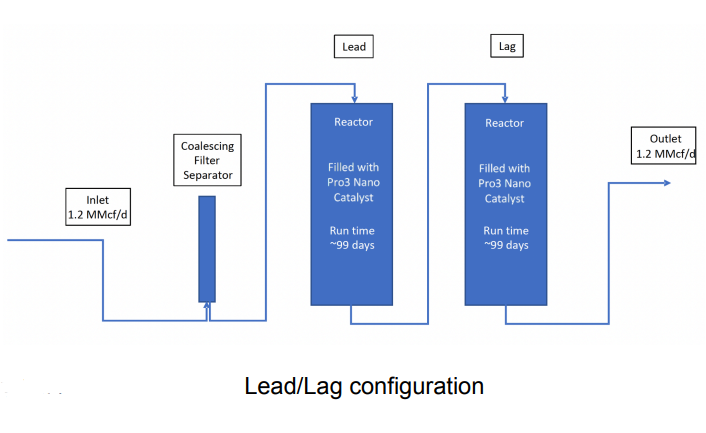
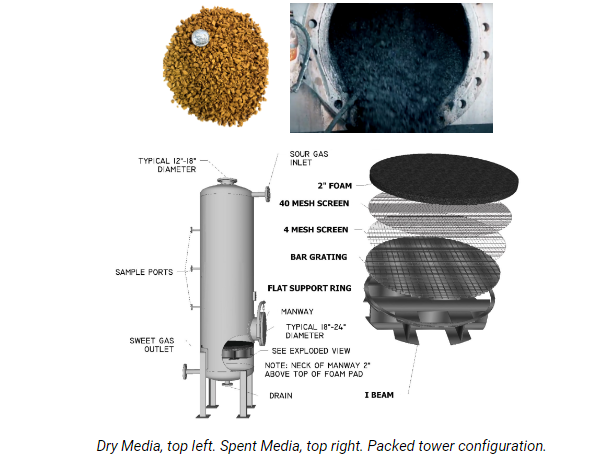
For the 1.2 MMscf/d example, we utilized a lead/lag configuration in our design. This setup included a coalescer upstream of the reactors which provided additional filtration. The lead/lag concept allows for continuous operations based on Q2 Technologies’ extensive field development program. Accounting for the expected breakover, the robust design of the lead/lag unit can be switched out so the lag reactor becomes the new lead reactor. The ability to swap reactors increases the bed life of the overall catalyst system.
Result:
- Natural Gas was sweetened to less than 4 ppm, achieving pipeline spec
- Run time of 99 days which is 3-5x longer performance than competitors.
- Safely removed 430 pounds of sulfur components per day.
Related Case Studies
Natural Gas - Triazine
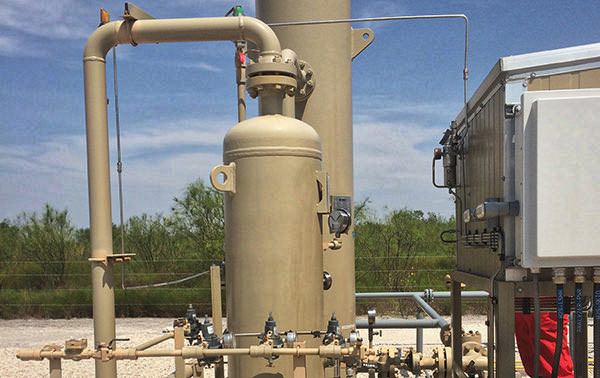
Natural Gas Processing Plant H2S Optimization Program
- Run times per chemical change-out increased by 35% by using Triazine.
Natural Gas - Triazine
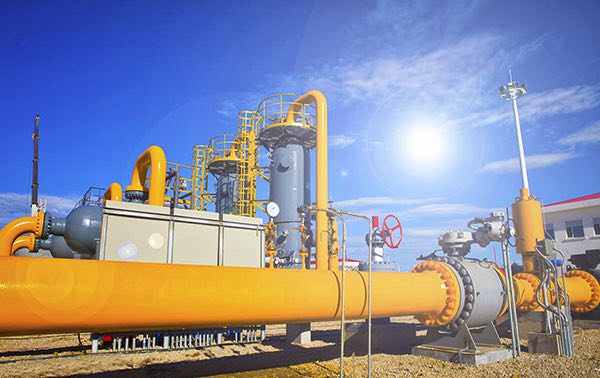
Natural Gas Treatment
- By using triazine, no solids were generated and only half the amount of Triazine was needed for treatment. compared to Sulfa-Check.
Natural Gas - Pro3® GT+
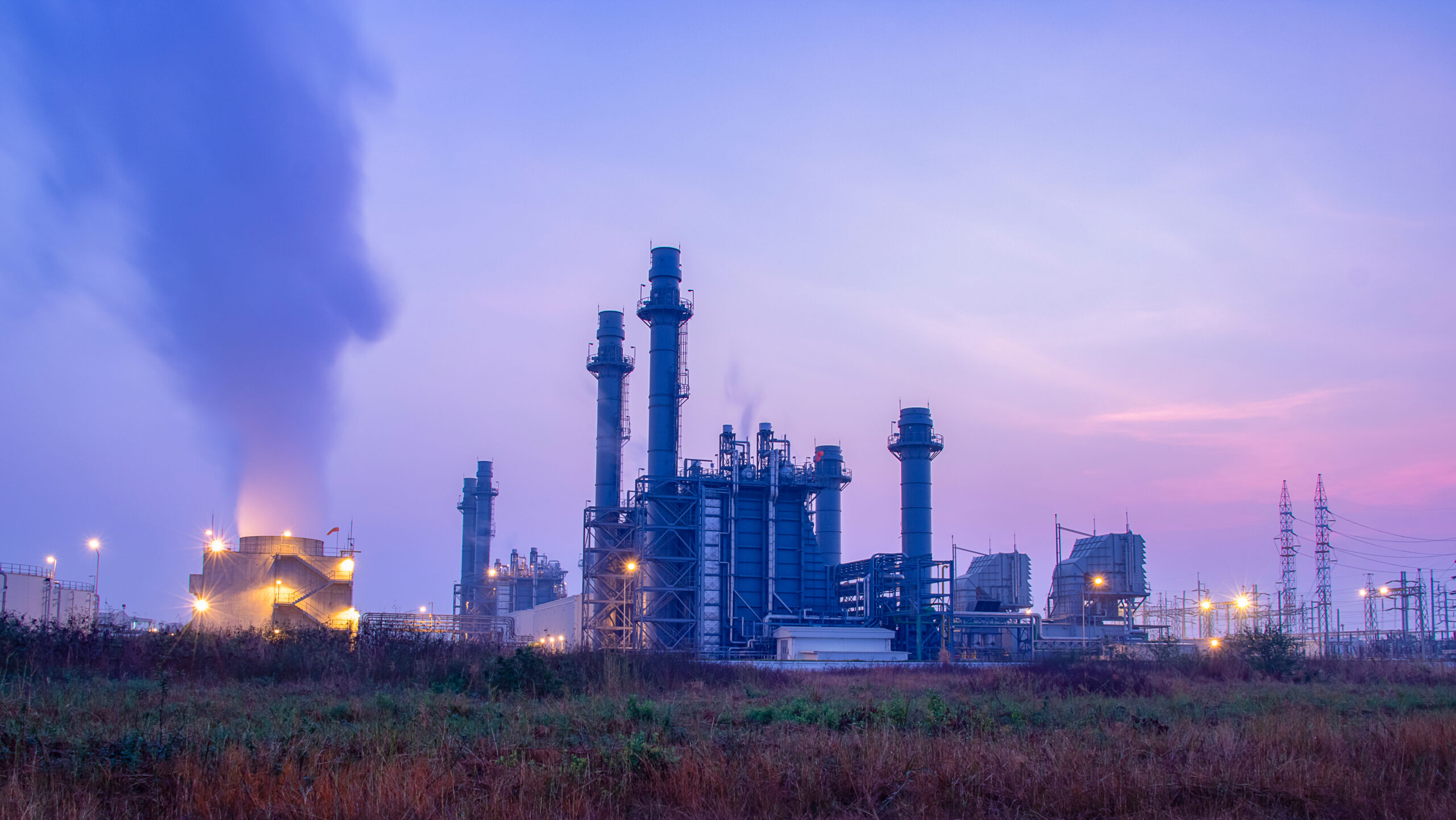
A direct substitute for triazine with seamless infrastructure integration.
- Pro3® GT+ surpasses traditional triazine scenarios with its faster reactions and increased capacity. It avoids scale formation or buildup common with overspent or overdosed triazine.