Posts in Category: Crude oil and liquid hydrocarbons
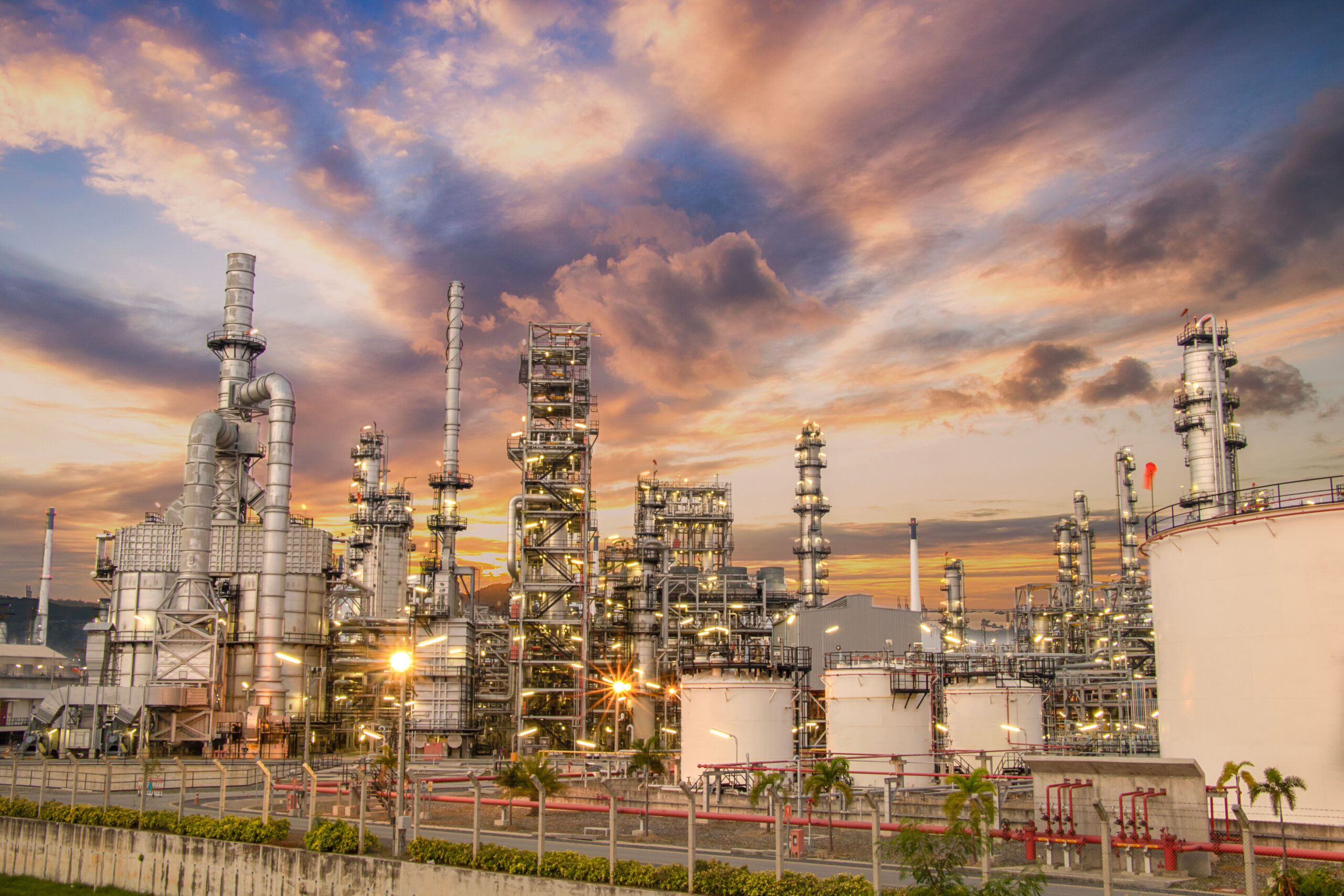
Understanding Lease Automatic Custody Transfer (LACT) Units in Midstream Operations
Learn how Lease Automatic Custody Transfer (LACT)…
Read more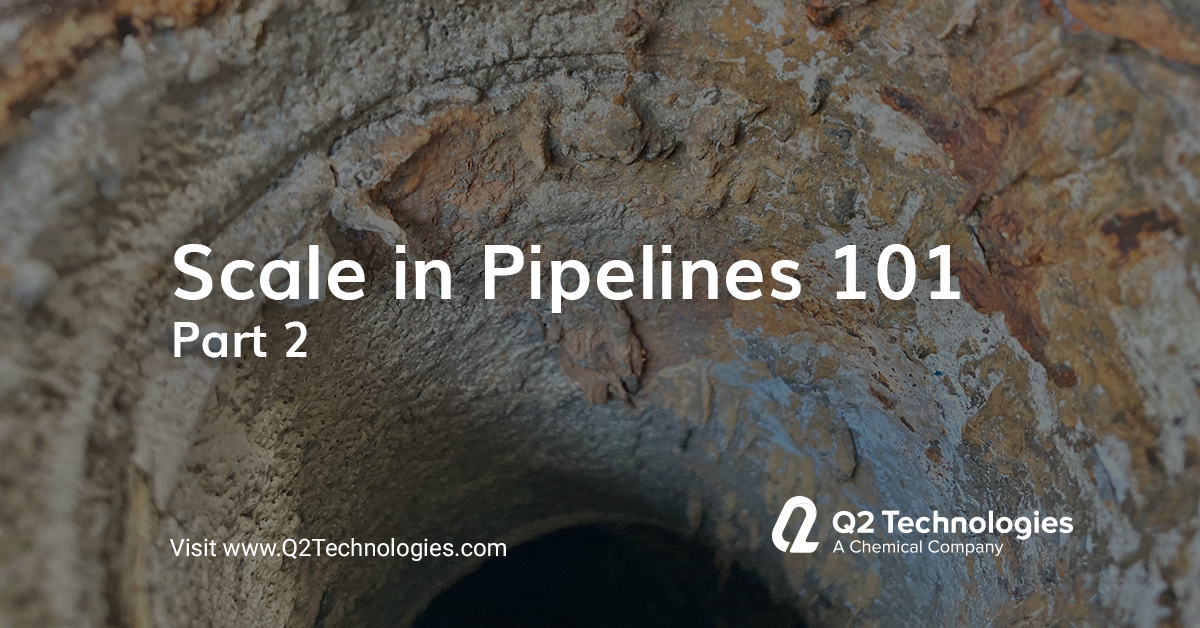
Scale in Pipelines 101 – Part 2
In this blog, discover the specific causes…
Read more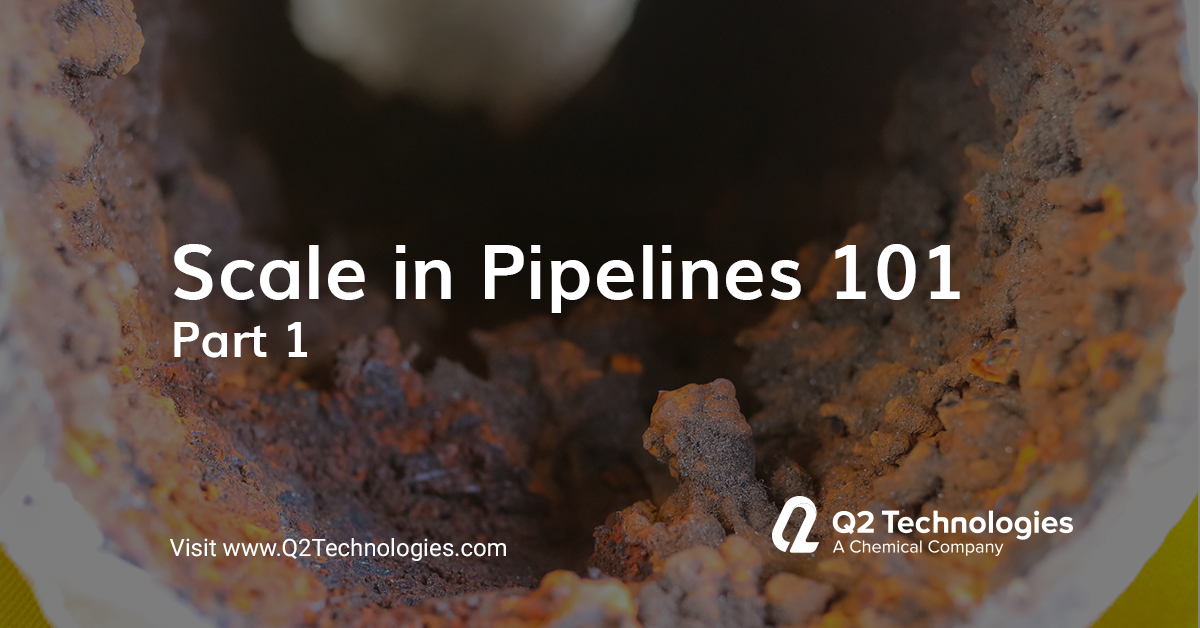
Scale in Pipelines 101 – Part 1
Scale. This sneaky accumulation of mineral deposits…
Read more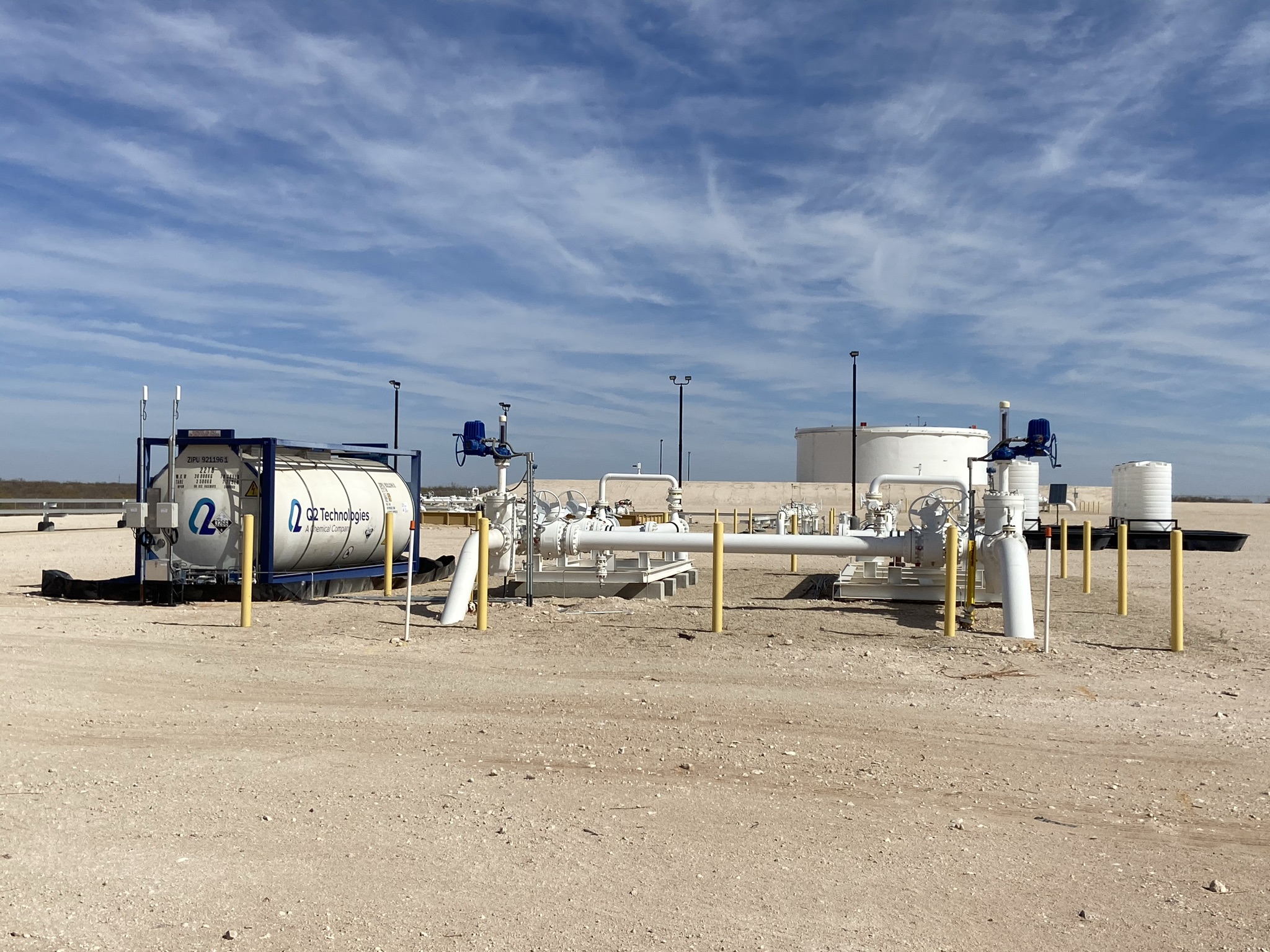
The Science of H2S Removal: Our Oilfield Chemical Solutions
We understand the importance of removing H2S…
Read more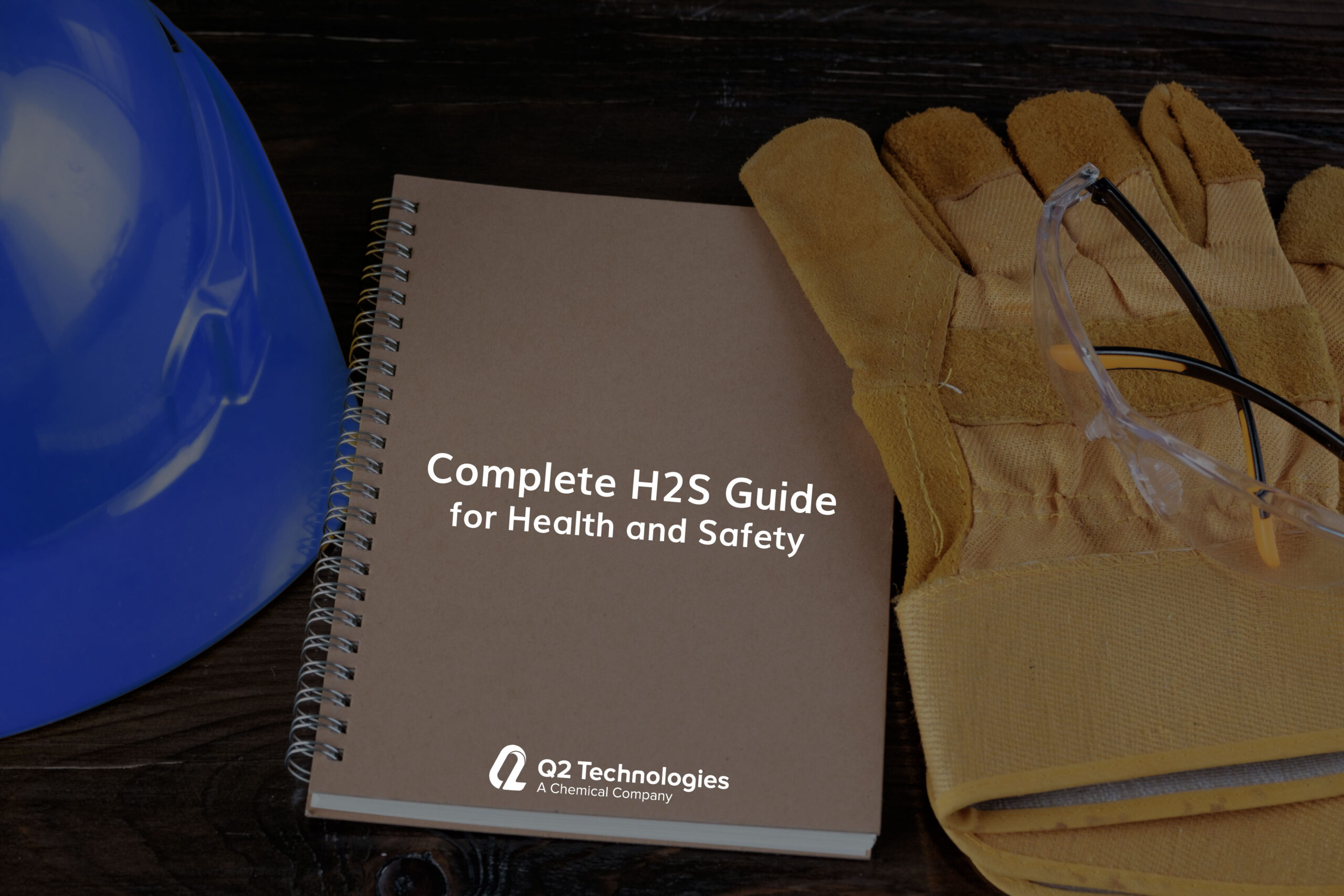
Complete H2S Guide for Health and Safety
The presence of H2S in Crude Oil…
Read more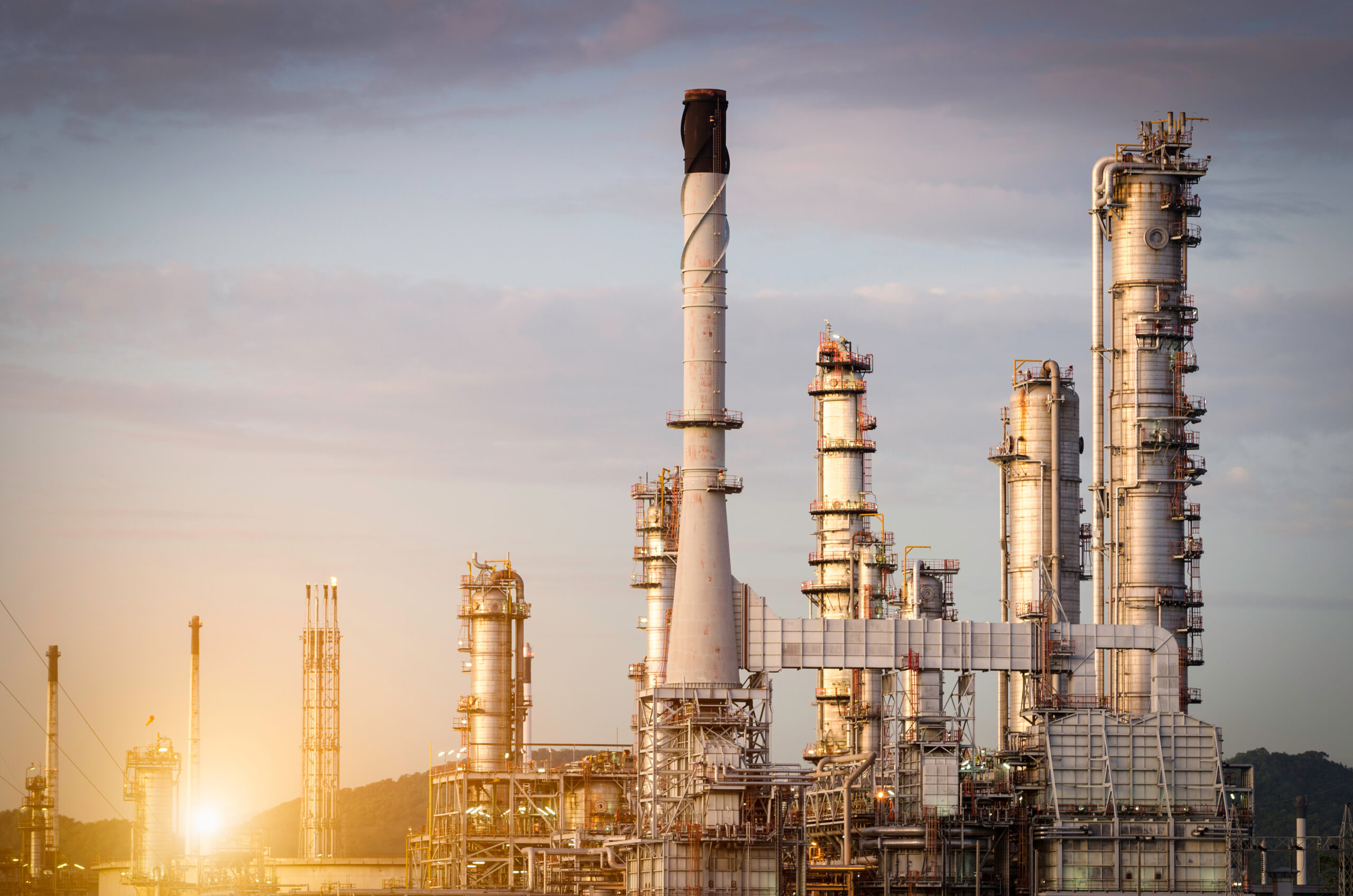
Cracking the Code on Treating H2S: Q2 Technologies’ Non-Triazine Scavengers Reducing Chemical Use Up to 75%
Non-triazine and non-amine H2S scavenger for Crude…
Read more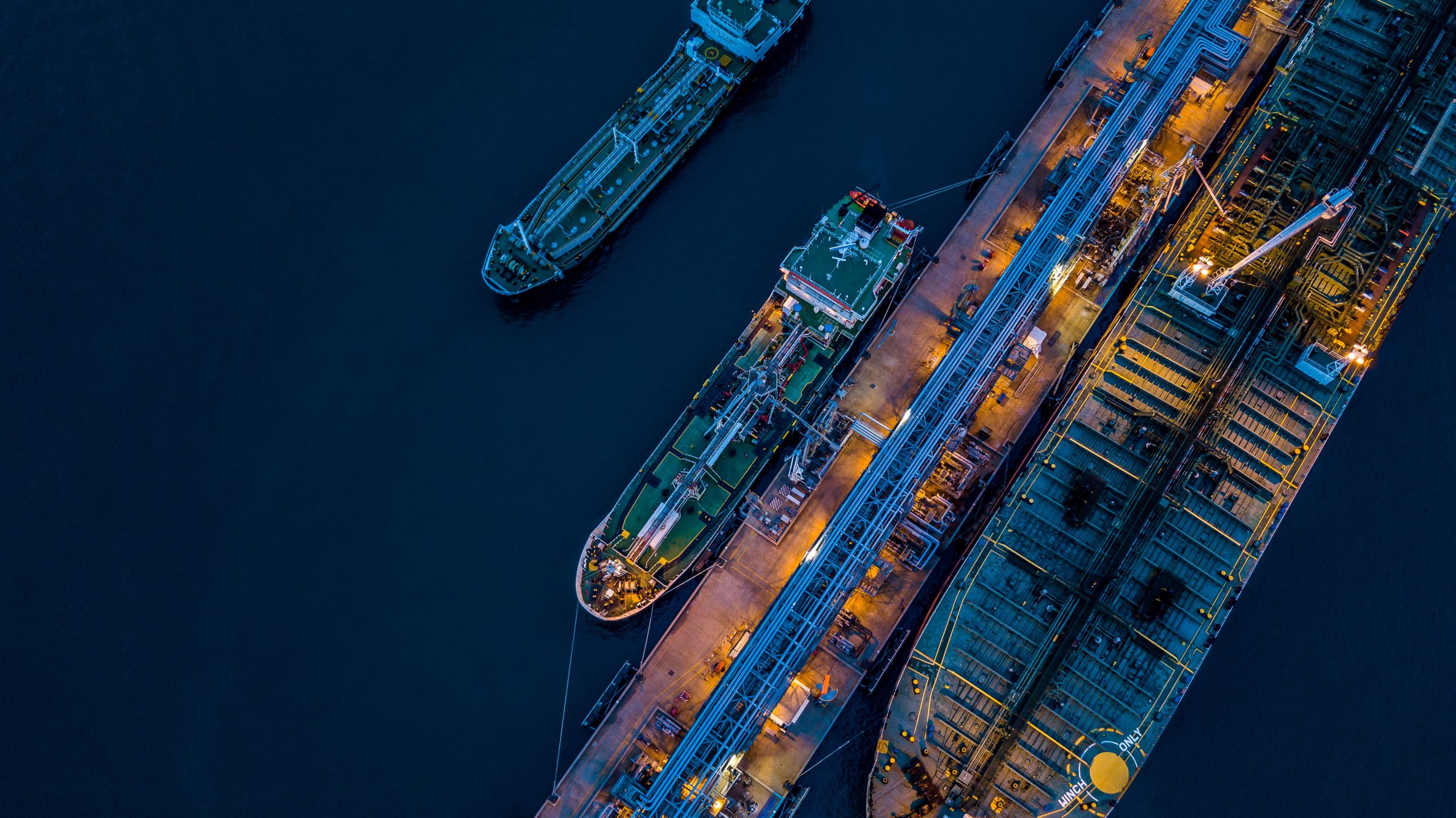
Removing Mercaptans While Keeping Costs in Line
Since mercaptans are highly complex branched sulfur-based…
Read more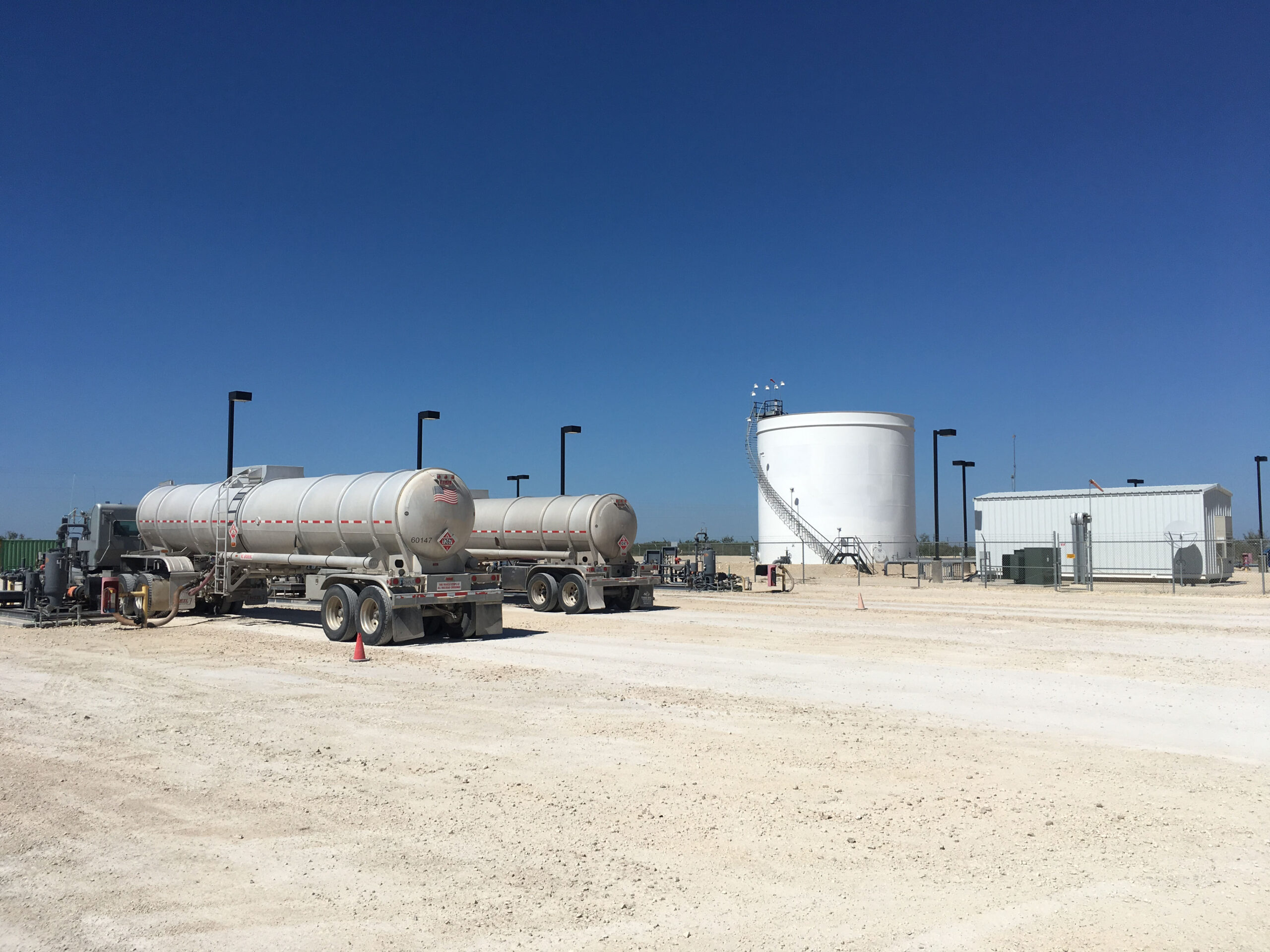
Treating Trucked Sour Crude
Barrels that have moderate to high levels…
Read more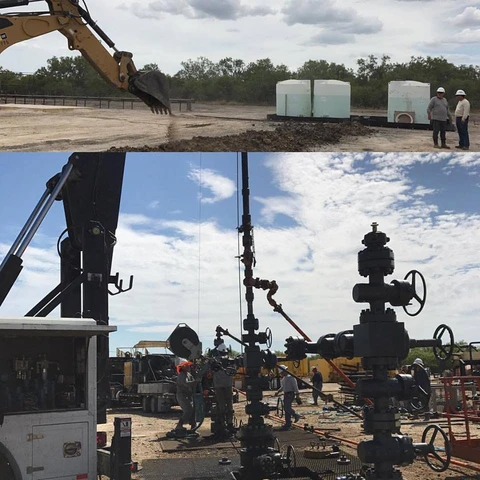
PRO3® Non-Amine Scavenger Process in the Eagle Ford Shale
Another PRO-3™ Non-Amine H2S Scavenger Process up…
Read more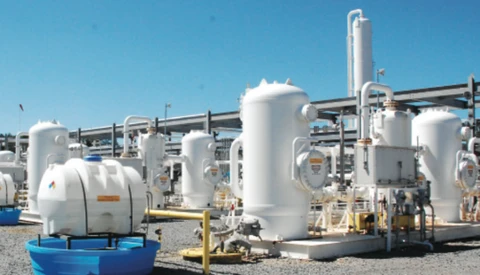
Q2 Technologies Brings Innovative Non-Amine/Non-Aldehyde Scavenger for Crude Oil
ENVIRO-SOLVE PRO3 is a non-fouling, water-soluble, oil-dispersible…
Read more